Engineered solutions refer to designing and developing custom parts to meet specific needs. To meet the required specifications, the components are designed and manufactured using advanced techniques — including computer-aided design (CAD) and computer-aided manufacturing (CAM). Engineered solutions are used in various industries, such as automotive, aerospace, construction, and energy.
Principal Manufacturing Corporation is a full-service supplier of engineered solutions for automotive, industrial, and OEM companies worldwide! We are an IATF 16949:2016 and ISO 14001:2015 certified company, and we maintain strict compliance with the International Traffic In Arms Regulations (ITAR).
Since 1996, we have been operating from our current 170,000 sq. foot facility in Broadview, IL. Our success can be attributed to our vast in-house tooling and the engineering assistance we offer our clients. In addition, our innovative solutions help our customers reduce costs and improve speed to market.
Automotive Engineered Solutions
The automotive industry relies heavily on producing high-quality, precision parts to ensure the safety and reliability of vehicles. To meet this demand, here is the list of automotive engineered solutions that have been developed to provide cost-effective ways to manufacture complex parts:
Fineblanking
Fineblanking is a precise manufacturing process used in the automotive industry to make complex and accurate parts with tight tolerances. It’s an economical alternative to conventional machining and is commonly used to make transmission, brake, and engine components.
Conventional Stamping
Conventional stamping produces simple, flat parts at a lower cost than other manufacturing methods. As a result, this process is often used to mass-produce automotive parts, such as body panels, brackets, and fasteners.
Plastic Injection Molding
Plastic injection molding is a favored manufacturing process in the automotive industry as it can rapidly and inexpensively produce intricate plastic parts. This method creates components like closure systems, seating, and headrests.
Automated Assembly
The automotive industry often utilizes automated assembly to rapidly produce large quantities of parts with consistently high quality. It employs machines to assemble various components into a complete product. It is highly efficient, reducing labor costs and increasing productivity.
Industrial Engineered Solutions
In the industrial sector, various processes manufacture complex parts with high precision. These processes are essential for producing high-quality components that meet strict industry standards. Here are some of the common industrial-engineered solutions used for this purpose:
CNC Machining
By inputting precise measurements and specifications, CNC machining can produce complex parts with exceptional precision and consistency.
Counterboring
Counterboring is a process that enlarges an existing hole to a specific depth and diameter. This precise drilling method is used in the industrial sector for precision hole-making. It ensures that the final product will meet the necessary specifications and requirements.
Deburring
Deburring involves removing sharp edges or burrs from metal parts. These burrs can not only affect the quality of the product but also pose safety risks to the end-user.
Grinding
A commonly used process in industrial manufacturing, grinding is a precise and efficient way of removing material from a workpiece using a rotating abrasive wheel.
Milling
Milling involves using a rotating cutting tool to remove material from a workpiece. This highly versatile method is often employed to create intricate and complex parts.
OEM Engineered Solutions
Here are some of the most common OEM-engineered solutions:
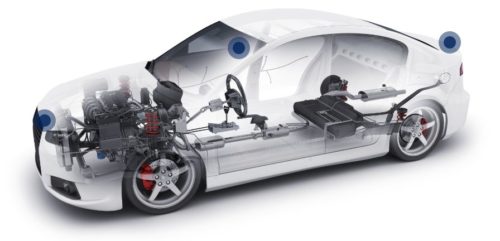
Orbital Riveting
Combining two parts using a circular motion can be accomplished with orbital riveting. This process is widely used by OEMs to connect different components, ensuring a secure and reliable joint.
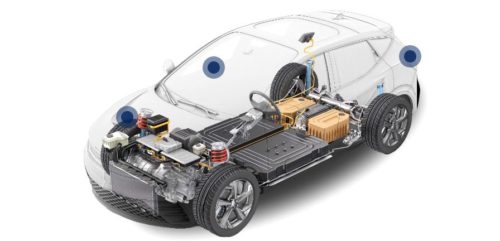
Staking
Staking is the preferred method to create a permanent connection between two components. This procedure deforms one of the components, forming a robust connection. It is commonly used by OEMs for high-strength applications.
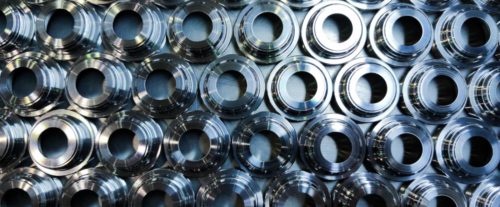
Tapping
Tapping is a process that uses cutting tools to start threads on a workpiece. This method is used in the OEM sector for creating threaded components, such as screws and bolts.
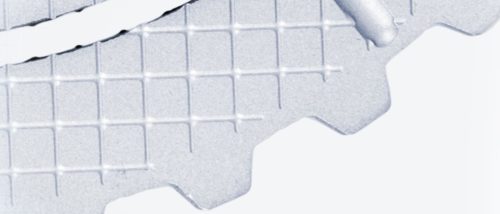
Turning
Removing material from a rotating workpiece using a cutting tool is called turning. This process is utilized by OEMs to create high-precision parts with tight tolerances.
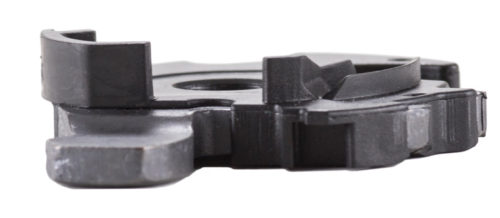
Vibratory Tumbling
Polishing and deburring metal parts can be done using vibratory tumbling. This method improves the overall surface finish of features, ensuring they meet quality standards.
Benefits of Engineered Solutions
Engineered solutions offer several benefits to industries, including the following:
Why Partner With Principal Manufacturing for Engineered Solutions
At Principal Manufacturing, we provide top-quality engineered solutions tailored to each business’s unique needs. Our offerings include fine blanking up to 700 tons, conventional stamping up to 400 tons, and plastic injection molding. Furthermore, our secondary operations include the following:
- Automated assembly
- CNC machining
- Counter boring
- Deburring
- Drilling
- Grinding
- Milling
- Orbital riveting
- Staking
- Tapping
- Turning
- Vibratory tumbling
Here are some reasons why partnering with us can benefit your business:
Experience and Expertise
Our team of highly skilled engineers and technicians have years of experience in the industry. Thus, we use the latest technology to deliver top-quality engineered solutions that exceed our customers’ expectations.
Innovative Solutions
We always look for new and innovative ways to improve our processes and deliver better customer results. We utilize cutting-edge technology and state-of-the-art equipment to create efficient and cost-effective solutions while maintaining the highest level of quality.
Personalized Service
Principal Manufacturing’s team is dedicated to providing exceptional customer service and support, from initial consultation to final delivery. Thus, we work closely with our clients to provide personalized solutions that meet their needs.
Continuous Improvement
We are committed to continuous improvement and always strive to find ways to improve our processes and solutions. Similarly, we welcome feedback from our clients and use it to drive our innovation and improvement efforts.
Quality Assurance
At Principal Manufacturing, we have a strict quality control process to ensure that every solution we deliver meets the highest quality standards. Our team conducts thorough testing and inspections throughout production to identify and resolve any issues before delivery.
Timely Delivery
We understand the importance of timely delivery and strive to deliver solutions on schedule without compromising quality.
Competitive Pricing
We understand that cost is a critical factor for businesses, and we are committed to providing our clients with competitive pricing for our engineered solutions. We will collaborate with you to find the best solutions that meet your needs and fit your project budgets.
At PMC we pride ourselves on adhering to the highest industry standards to ensure the quality of our products and sustainability of our operations. Our commitment is reflected in our globally recognized certifications, IATF16949:2016 for automotive quality management and ISO14001:2015 for environmental management. Additionally, we maintain strict compliance with the International Traffic In Arms Regulations (ITAR) showcasing our commitment to safeguarding sensitive information and technology.
If you want to learn more about how Principal Manufacturing Corporation can provide engineered solutions for your business, please don’t hesitate to contact us today.